RAJASTHAN - THE ADVENTURES OF PRINTING
Fabric printing is an Indian specialty, with woodblock printing probably being used for about 400 years. The process itself requires a great deal of patience.
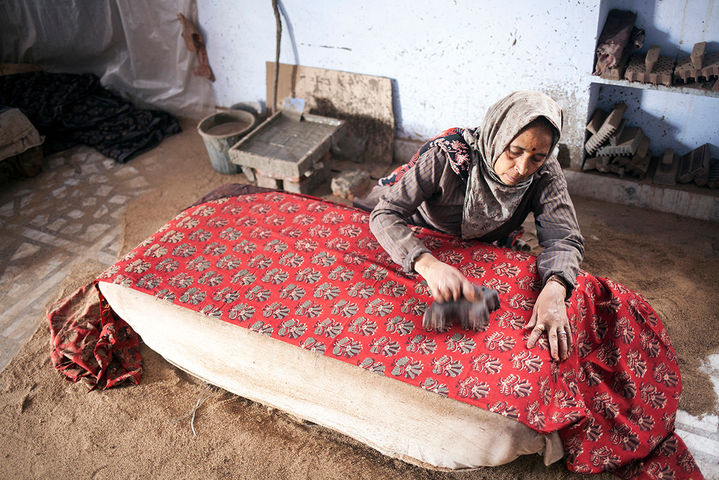
The Family Color Shade
Bagru is a town in the desert of Rajasthan, near Jaipur. Bagru is famous for printing exclusively with natural dyes. The main experts are members of the Chippa community. (Chi – to dye, pa – to dry something in the sun). They pass down their tradition and workshops through generations, training and perfecting the techniques of woodblock printing and dye usage within their families. Each family has its own recipe for natural color tones, which they closely guard.

Sand and Drought
A highway from Jaipur leads to Bagru, cutting through the desert towards the neighboring state of Gujarat. As soon as we turn off the main road, we find ourselves in the heart of traditional rural life. Children in school uniforms walk to school, and wedding processions of women in colorful sarees cross the road. Long strips of fabric hang from the houses in the village square, drying under the scorching sun. The dryness here is a concern, as without water, this craft could easily disappear. Water is mostly supplied by tankers.

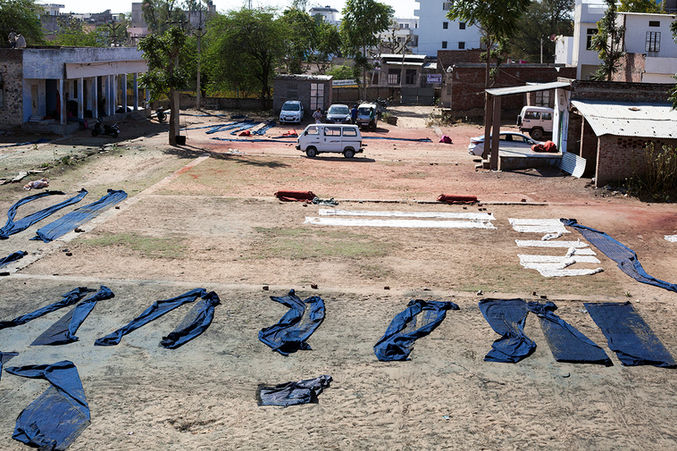
A Museum of Traditions
Suraj Narayan Titanwala fulfilled his dream and opened a woodblock printing museum on his property at the end of February, showcasing rare fabric exhibits and blocks made two hundred years ago. "The museum is an effort to preserve the art of traditional printing in Bagru," says Titanwala.


Printing Paste
Titanwala takes me to a printing workshop called Dhabu, a place where printing is done using mud paste. The process is completely different. I kneel on the ground at a small table. It's dimly lit, with sawdust and dust on the floor, a pleasant coolness in the air. To my right, there's a container of mud. I begin dipping the blocks into the mud and printing. Unlike using dye, it’s harder to maintain precision here, as the mud is very fluid and drips from the blocks. What is now printed on the fabric with the mud will ultimately be white. Once I’ve printed a piece of fabric, I must sprinkle it with sawdust to stabilize the mud. Unlike regular printing with dyes, the entire print cannot be seen all at once. Locals estimate that there are about 200 printing houses in Bagru and the surrounding area that dye using mud paste, natural rubber, and wheat flakes. Organic base colors are derived from natural materials such as tamarind, alum, indigo, and even pomegranate, along with other fruits and vegetables.

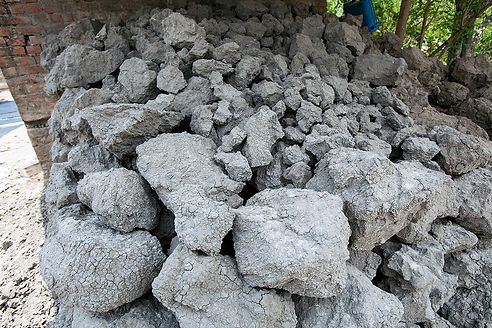
Unique Fabrics
This is the slowest and most complicated fabric printing process, but it is also environmentally friendly. In ancient times, fabrics from Bagru were part of dowries and were highly valued originals that families literally revered. The uniqueness of each piece of fabric was used as decoration for wedding ceremonies and displayed as tapestries in the palaces of royal families in Rajasthan. Imagine, making a single cotton bedspread can take 26 days and goes through 15 different procedures.



